The Tinsley Belt Coater produces the highest quality chocolate coated product because of our built-in
features:
- Belt widths of 24”, 48”, 60” and 74” for production outputs of 200-800 lbs./hr. depending on product density and ratio to chocolate.
- Load cell weight control with +/- of one (1) pound product weight using the Allen-Bradley Processor.
- PLC Processor controlled chocolate feed of 6-8 lbs. per cycle through 3mm diameter drip nozzles, installed at 3” centers. This provides a uniform chocolate coating with little spillage onto the belt, reducing doubles and multi-clusters of product.
- An auxiliary water heater within the jacketed header tube will keep the melted chocolate temperature uniform for feed and drip through each nozzle.
- A heated scraper blade returns the chocolate in liquid form back into the processed product without creating multiple clusters, removing the excess chocolate from the belt surface.
- A bottom belt scraper will remove more of the belt surface particles and drop them into a floor supported collecting pan, not affecting the load cells. The collecting pans will easily roll out for cleaning.
- Our high rate of cooling air supplied to the coated product between each chocolate supply cycle will reduce the chocolate cooling, drying and curing time, increasing output.
- By using the two chocolate valve feed control system, (one in the supply line and one in the return line), you are assured a good chocolate feed pressure within the header tube and through each drip nozzle. During the off chocolate drip cycle, the return valve opens and allows the chocolate to flow back to the melting tank for recycling.
- Made of heavy-duty tubular stainless steel, our construction keeps vibration to a minimum.
- Drive motor controlled via variable frequency speed controller for belt speed adjustment from 0-200 FPM. This will allow for excellent product tumble and uniform product coating at its proper belt speed for the different products.
- The food-grade, UHMWP, heavy-duty plastic belt is a flat surface and easier to clean or wash down. It offers positive traction control and an extremely long operating life span.
- The Master Control Panel can be rotated away from the back wall for easy access to the removable back panels of the machine.
- Access the water-jacketed chocolate feed header by removing the back half of the top cover.
- An interior light will light up the product processing area for easy inspection during the coating.
- Lexan front doors will allow for easy product access and inspection.
- Fully automated PLC controlled belt coater can be connected to a bucket conveyor to move the finished product to the cooling room and the belt polisher.
- Melting tanks with complete piping system available from 500 to 20,000 lbs. Piping system can be ordered separately to your specifications.
- 74″ Belt Coater – 400-800 LBs/HR, 105″ long x 76″ deep x 86″ height; about 3,200 pounds
- 60” Belt Coater – 300-600 LBs/HR, 92” long x 76” deep x 86” height; about 3,000 pounds
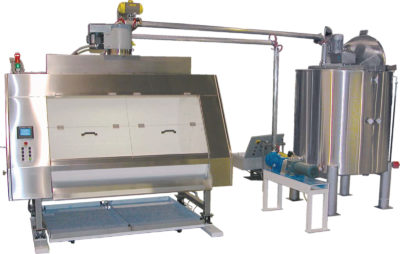
TINSLEY CHOCOLATE AUTOMATION LINE 74” COATER, 6,000 LB TANK & CHOCOLATE PUMP

CONTROL CABINET WITH PROGRAMMABLE CONTROLS
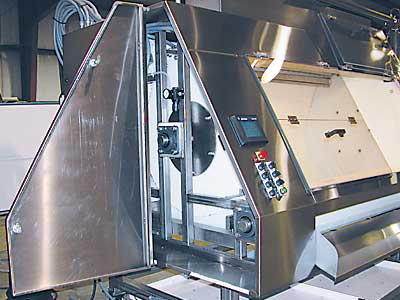
EASY ACCESS FOR CLEANING
![]() |
COATER BROCHURE |
DOWNLOAD PDF |
![]() |
COATER SPECS |
DOWNLOAD PDF |